PCB MANUFACTURING
A & P Material Supply is Your Trusted PCB Supply Partner. A & P Material Supply is a leading provider of high-quality printed circuit boards, offering state-of-the-art manufacturing facilities, experienced professionals, and customized solutions to meet the unique needs of our clients. We stay at the forefront of technological advancements in the PCB industry, constantly investing in the latest equipment and processes to deliver cutting-edge solutions.
PCB SOLUTIONS
A & P Material Supply offers a wide range of PCB solutions, from simple single-layer boards to advanced multi-layer and HDI designs.
MINIMIZE YOUR COSTS
We work closely with our clients to understand their unique requirements and provide customized solutions that optimize functionality while minimizing costs.
SOLUTIONS THAT LAST
We stay at the forefront of technological advancements in the PCB industry, constantly investing in the latest equipment and processes to deliver cutting-edge solutions.
Printed Circuit Boards
Printed circuit boards (PCBs) are the foundational building blocks of virtually all modern electronic devices. They provide mechanical support and electrical connections for electronic components using conductive pathways, tracks, or signal traces etched from copper sheets laminated onto a non-conductive substrate. The substrate layer is typically made of fiberglass, which provides rigidity and strength to the PCB.
PCBs offer numerous benefits that make them indispensable in the electronics industry. Their compact design allows for the miniaturization of devices, enabling the creation of smaller, more portable products that can be easily integrated into our daily lives. The use of PCBs also improves signal integrity, as the precise layout and routing of traces minimizes interference and ensures reliable data transfer.
How are Printed Circuit Boards Used?
As technology continues to advance at a rapid pace, the PCB industry must constantly evolve to keep up with the growing demands for faster, smaller, and more complex devices. The rise of 5G networks, the Internet of Things (IoT), and artificial intelligence (AI) has driven the need for high-density interconnect (HDI) PCBs, which feature finer pitch sizes and more layers to accommodate the increased complexity of modern electronics.
"PCBs are the unsung heroes of the modern world, enabling the technological marvels we rely on every day. From smartphones and laptops to medical devices and aerospace systems, PCBs form the backbone of countless electronic devices."
History of Printed Circuit Boards
The history of PCBs is a fascinating journey that spans several decades. The origins of PCBs can be traced back to the early 20th century when the electronics industry was still in its infancy. A significant breakthrough came with the development of wire wrapping, a technique where small gauge wires were tightly wrapped around posts at each connection point, creating gas-tight connections that were highly durable and easily changeable.
The advent of PCBs revolutionized the electronics industry by providing a compact, reliable, and cost-effective means of interconnecting electronic components. The first PCBs were developed in the 1940s and 1950s, with early designs featuring copper traces etched onto a non-conductive substrate such as Bakelite or phenolic resin.
Different Types of Printed Circuit Boards
PCBs come in a wide variety of types, each with its own unique characteristics and applications. The most common types of PCBs include single-sided, double-sided, and multi-layer boards. Single-sided PCBs have components mounted on one side of the board, with the other side typically serving as a ground plane. Double-sided PCBs, on the other hand, utilize both sides of the board for mounting components, with each side acting as a signal layer.
At A & P Material Supply, we take pride in our ability to handle a wide variety of PCB types, including rigid, flex, and rigid-flex designs, as well as specialized materials like metal-core and high-temperature laminates. Our expertise in HDI technology allows us to create highly compact and dense PCBs that are essential for the development of advanced electronic devices in industries such as telecommunications, aerospace, and medical equipment.
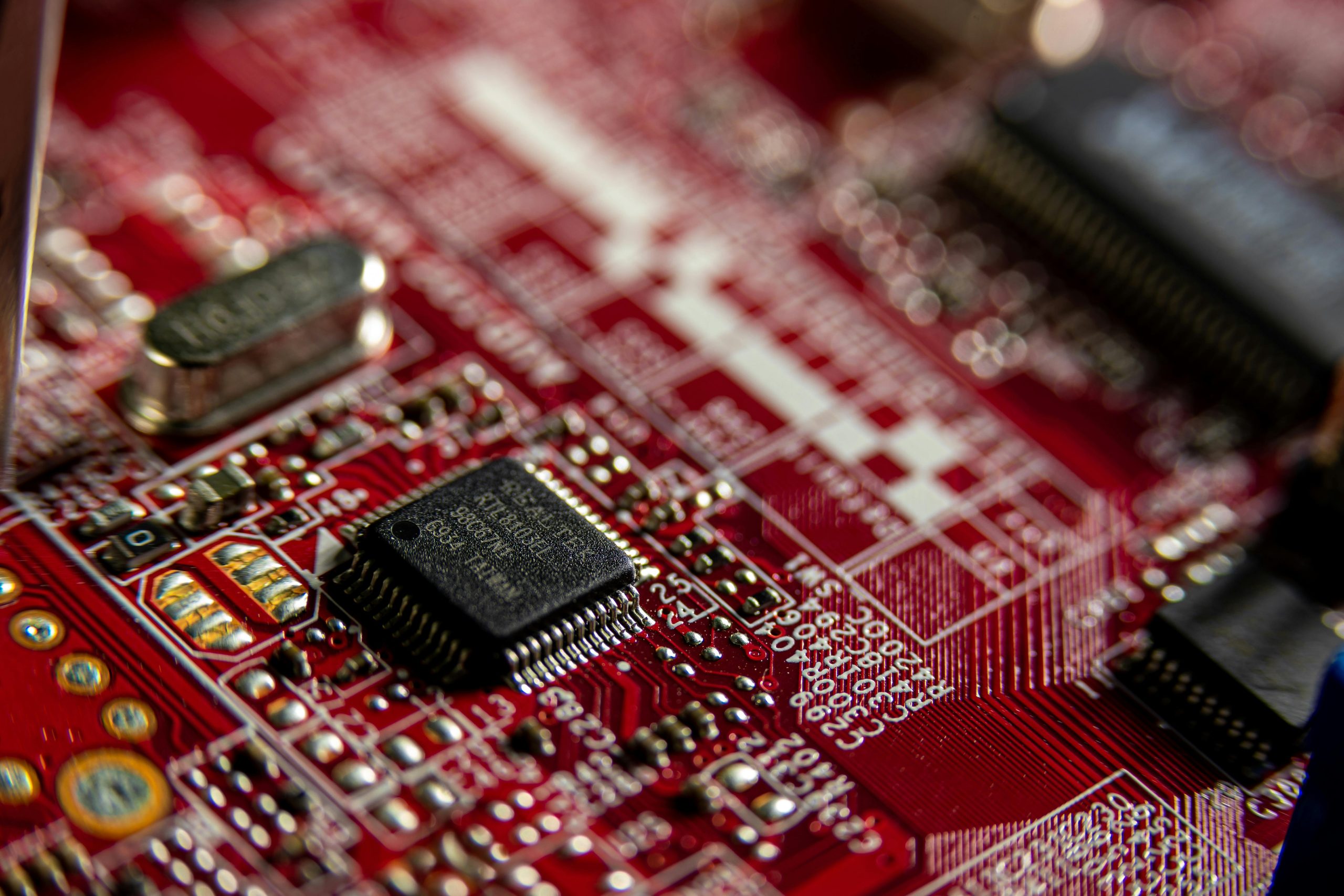
PCBs are composed of several essential components that work together to enable the functionality of the device. The primary elements include the substrate layer, copper layer, solder mask layer, and silkscreen layer.
List of Essential Components
- Substrate layer: Forms the foundation of the PCB, providing rigidity and strength. Typically made of fiberglass, such as FR-4.
- Copper layer: Laminated on top of the substrate, creating the conductive pathways that carry electrical signals between components.
- Solder mask layer: Covers the copper layer, insulating the copper traces from accidental contact with other conductive materials.
- Silkscreen layer: Applied on top of the solder mask, adding text, numbers, and symbols to aid in assembly and indicate component functions.
Functions of Each Component
The substrate layer serves as the foundation of the PCB, providing mechanical support and insulation between the conductive layers. The copper layer is responsible for creating the conductive pathways that carry electrical signals between components. The solder mask layer insulates the copper traces from accidental contact with other conductive materials, prevents short circuits, and protects the copper from oxidation and corrosion. The silkscreen layer adds text, numbers, and symbols to the PCB, aiding in the assembly process and providing component reference designators, polarity indicators, and other important information.
How Components are Connected
The components on a PCB are connected through a network of copper traces, pads, and vias. Traces are the thin, flat pathways that carry electrical signals between components. Pads are the exposed metal areas where components are soldered to the board. Vias are small holes drilled through the PCB that allow signals to pass from one layer to another.
Common Problems with Components
PCBs are not immune to problems that can arise during manufacturing or use. One of the most common issues is the presence of defects in the PCB components, such as solder bridges, voids, or tombstoning. These defects can cause short circuits and other electrical issues that interfere with the proper functioning of the board.
Signal integrity issues are another common problem in PCB design. As electronic devices become faster and more complex, the risk of signal degradation and interference increases. Proper routing techniques, such as avoiding long parallel traces and using ground planes to shield signals, can help minimize crosstalk and ensure reliable signal transmission across the board.
The PCB manufacturing process is a complex and precise endeavor that requires a high level of expertise and attention to detail. From the initial design phase to the final assembly, each step plays a crucial role in determining the quality and reliability of the finished product .
Step-by-Step Manufacturing Process
- Design: The process begins with the creation of a schematic, which outlines the electrical connections between components. This schematic is then translated into a physical layout, where the placement of components and routing of traces are carefully optimized to ensure optimal performance.
- Material Selection: One of the most critical aspects of PCB manufacturing is the selection of materials. The substrate, typically made of fiberglass, provides the foundation for the board and determines its rigidity and strength. The copper layer, which is laminated to the substrate, forms the conductive pathways that carry electrical signals between components.
- Printing and Etching: The inner layers of the PCB are first printed onto a thin film, which is then aligned with the substrate using registration holes. The film is exposed to ultraviolet light, hardening the areas that will form the conductive pathways. The unexposed areas are then washed away, leaving behind the desired circuit pattern.
- Lamination: This process is repeated for each layer of the PCB, with the layers being laminated together under high pressure and heat to form a solid board.
- Drilling and Plating: Once the PCB has been laminated, it undergoes a series of drilling and plating processes to create the necessary holes and vias that connect the layers.
- Outer Layer Processing: The outer layers of the board are then etched, removing the excess copper to reveal the final circuit pattern. A solder mask is applied to protect the copper traces, and a silkscreen layer is added to provide component labels and other identifying marks.
- Quality Control: Finally, the board undergoes a series of quality control tests to ensure that it meets the required specifications and is free from defects.
Tools and Materials Required
Crafting a printed circuit board requires a variety of tools and materials to transform the design into a functional, physical product. The essential components include the substrate layer, copper layer, solder mask layer, and silkscreen layer. To manufacture a PCB, various tools and equipment are required at each stage of the process, such as PCB design software, photoresist and UV light exposure equipment, etching equipment, laminating equipment, drilling machines, plating equipment, and surface finishing equipment.
Safety Precautions during Production
Safety precautions during the PCB manufacturing process are paramount to ensure the well-being of workers and the quality of the final product. Proper handling and storage of hazardous substances are crucial to prevent accidents, injuries, and environmental contamination. Workers must be equipped with appropriate personal protective equipment (PPE) such as gloves, safety glasses, and respirators to minimize exposure to harmful substances..
Electrical safety is another critical aspect of PCB manufacturing. Proper grounding and ESD protection measures must be implemented throughout the manufacturing process. Fire safety is also essential, with fire suppression systems and worker training in place to ensure a swift and safe response in the event of a fire .
Quality Control and Testing
Quality control and testing are critical components of the PCB manufacturing process, ensuring that the final product meets the required specifications and performs as intended. At A & P Material Supply, we employ various techniques and tools to maintain strict quality control throughout the production process, such as automated optical inspection (AOI) systems, electrical testing methods, and environmental stress testing.
Effective collaboration between PCB designers and manufacturers is essential for ensuring the successful production of high-quality, reliable circuit boards. By working closely together, designers and manufacturers can identify and address potential issues early in the development process, reducing the risk of costly delays and rework [8].
PCBs are essential components in a wide range of applications, from smartphones and laptops to medical devices and aerospace systems. The demand for smaller, faster, and more powerful electronic devices has driven the need for high-density interconnect (HDI) PCBs, which feature finer pitch sizes and more layers to accommodate the increased complexity of modern electronics.
Use in Computers and Electronics
The use of PCBs in computers and electronics has revolutionized the way we live, work, and communicate, allowing for the development of increasingly compact, powerful, and interconnected devices. High-frequency PCBs, designed to operate at several gigahertz or higher, are crucial for applications such as telecommunications, microwave systems, and radar.
The development of HDI PCBs has been another game-changer in the electronics industry, enabling the creation of highly compact and complex devices. The rise of smartphones, wearable technology, and the Internet of Things (IoT) has driven the need for these advanced PCBs, as manufacturers strive to pack more functionality into smaller form factors.
Use in Telecommunications
PCBs play a crucial role in the telecommunications industry, enabling the rapid transmission of data and signals across vast distances.
The advent of 5G networks has further accelerated the demand for high-performance PCBs in the telecommunications industry. With data transmission speeds of up to 20 Gbps, 5G technology requires PCBs that can handle extremely high frequencies and maintain signal integrity across complex circuits. Mixed-signal PCBs, which combine analog and digital components, are particularly well-suited for 5G applications, as they enable low latency and extended connectivity reach.
Use in Automotive Industry
PCBs have become an integral part of the automotive industry, enabling the development of advanced electronic systems that enhance vehicle performance, safety, and user experience. As the demand for connected, autonomous, and electric vehicles continues to grow, PCBs play a crucial role in facilitating the integration of cutting-edge technologies.
The rise of electric vehicles (EVs) has also driven the demand for advanced PCBs in the automotive industry. EVs require sophisticated power management systems to control the flow of electricity between the battery, motor, and other components. These systems rely on PCBs with high current carrying capacity and thermal management capabilities to ensure optimal performance and longevity.
Emerging Trends in PCB Applications
The PCB industry is constantly evolving, with new technologies and trends emerging at a rapid pace. One of the most significant developments in recent years has been the rise of high-density interconnect (HDI) PCBs, which enable the creation of smaller, more compact boards with increased routing capabilities and faster signal transmission.
Another trend that is shaping the future of PCBs is the integration of the Internet of Things (IoT) and artificial intelligence (AI) technologies. IoT devices require PCBs that can handle high-speed data transmission and maintain signal integrity in a compact form factor, while AI is being used to optimize PCB manufacturing processes, improving quality control and reducing costs [8].
EMERGING
PCB TECHNOLOGIES
One of the most promising developments is the rise of 3D printing technology in PCB manufacturing. This additive manufacturing technique allows for the creation of complex, non-planar structures and streamlines the prototyping process. By depositing conductive and insulating materials layer by layer, 3D printing enables the fabrication of PCBs with intricate geometries and unique features.
Another area of focus is the integration of AI and ML into PCB design and manufacturing processes. AI-powered tools can analyze vast amounts of data to optimize layouts, identify potential issues, and improve overall efficiency. By leveraging AI and ML, manufacturers can enhance quality control, reduce human error, and adapt quickly to changing customer requirements